Born in the 1990s, the MES (manufacturing execution system) has gradually been adopted, somewhat like the ERPs that appeared in the previous decade. Put off by the budgets spent on ERPs, which they had not necessarily anticipated, companies have been more demanding when it comes to MESs, and mid-sized companies have lagged behind in adopting them.
Today, alongside products from major vendors and builders, agile solutions have been developed, offering a quick return on investment and a vast array of functionalities. But now that many mid-sized companies have finally added an MES to their budgets, the technologies of the industry of the future are giving them pause: are we not on the eve of a complete change in philosophy? What with IoT, cloud computing and big data, isn't it a better idea to wait? If you take a closer look, though, at the factory of the future, the original concept behind the MES is now coming back to the forefront...
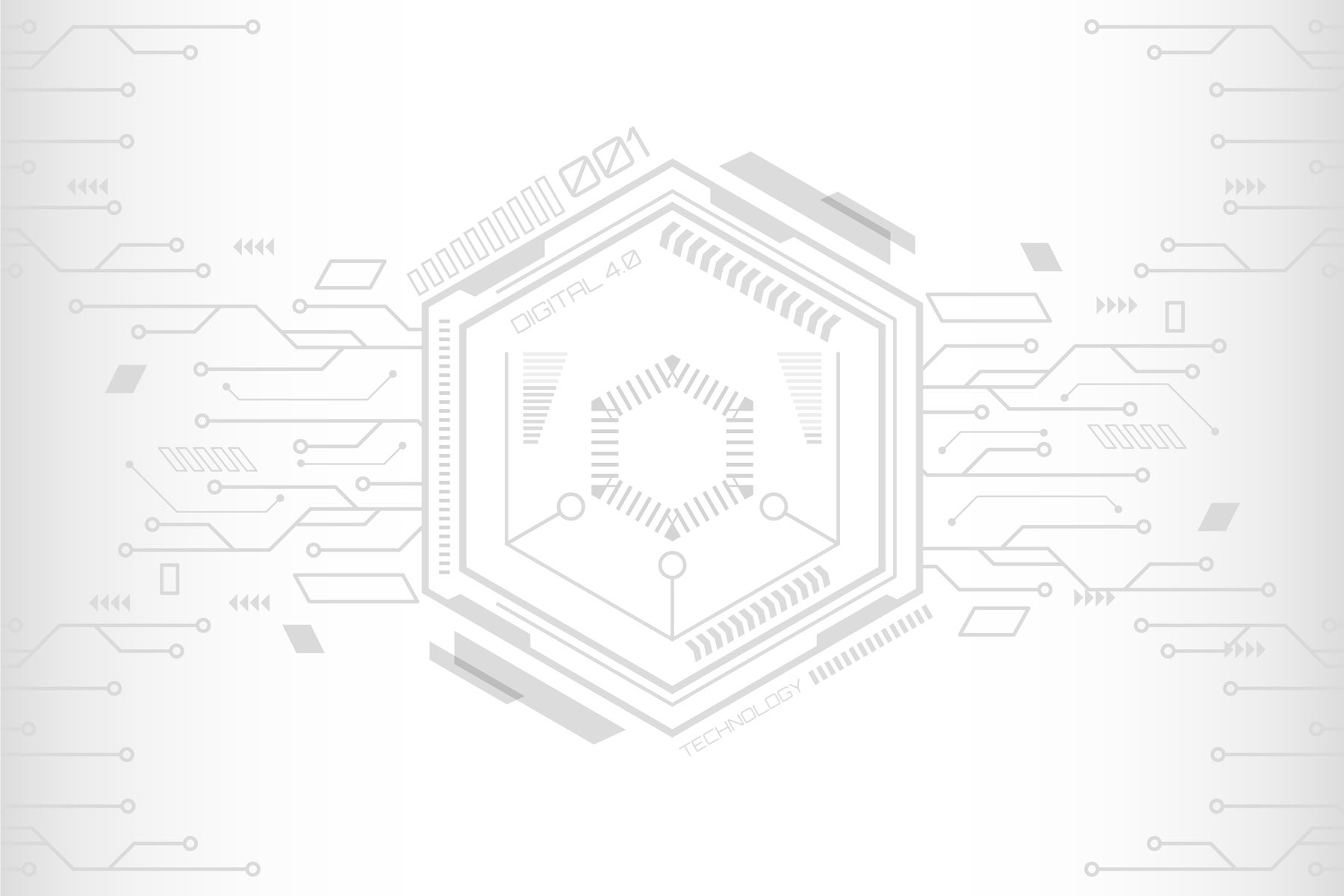
A Flood of New Technologies
Many technologies have been released at an unprecedented pace since the advent of the Internet some 20-odd years ago. So much so that we can't always remember the order in which they first appeared. SaaS (Software as a Service) probably kicked things off, followed by virtualization, cloud computing, the explosive success of cell phones and smartphones, tablets, and then 3D printing, big data, IoT, smart objects, artificial intelligence, and more.
Industry in the Line of Sight
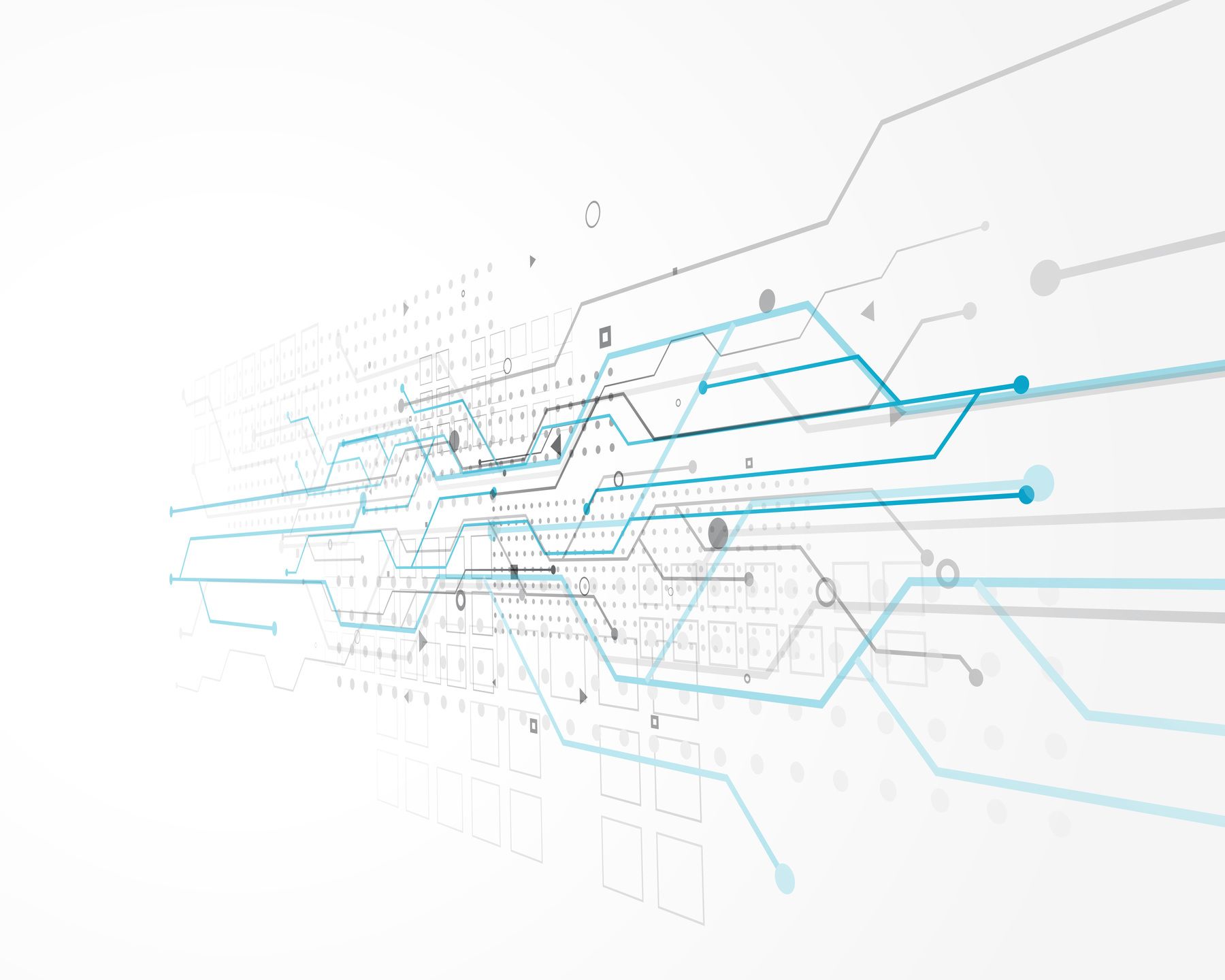
Truth be told, industrial companies did not initially feel themselves to be very concerned by the first technological waves: the concept od SaaS, for example, involving the substantial standardization of available software features, could be applied more easily to email and accounting than to the execution of industrial processes, which are very different in nature. Not to mention, of course, the criticality and confidentiality of manufacturing data.
3D printing played a revelatory role: recent technological innovations had the ability to overturn our whole conception of industry. From that point onward, new information technologies (cloud computing, big data, IoT, etc.) began to seek outlets outside the spheres of personal, financial and marketing uses. Robotics and artificial intelligence, both originating in the 1950s, have refreshed their images to join them: Industry of the Future is on the move.
What does this mean for MES?
In the face of this technological upheaval, some have suggested that the usefulness of MESs may be called into question. At first glance, this seems a bit strange, since no one has suggested, for example, that these technologies would challenge the use of ERPs. An MES, like an ERP, is not a technology, but rather a functional solution, so why would the new technologies of the industry of the future call it into question?
In fact, as has happened in the past, MESs suffer from a simplistic vision of their role. Remember the “link between the ERP and the field” that was ascribed to them. It’s true, of course, but if that were its only role, MESs would have lost all meaning, once ERPs gained the capacity to collect field information, which has long been a reality.
The same pitfall can be seen with the technologies of the industry of the future. IIoT (Industrial Internet of Things) will make it possible to collect more information, both inside and outside the factory, particularly about post-production product life cycles, amassing big data either locally or in the cloud. It’s easy to imagine a future in which smart equipment calculates its own MTBF (mean time between failures) or its down time, classified into categories. But in order to be usable, that information needs to be cross-referenced with the types of products manufactured, the manufacturing orders in progress and the teams involved in the production process, so as to yield relevant production indicators (OEE, OOE, TEEP and other KPIs). Within this contextualization and consolidation, the MES still has a place.
The MES: The Heart of the Industry of the Future
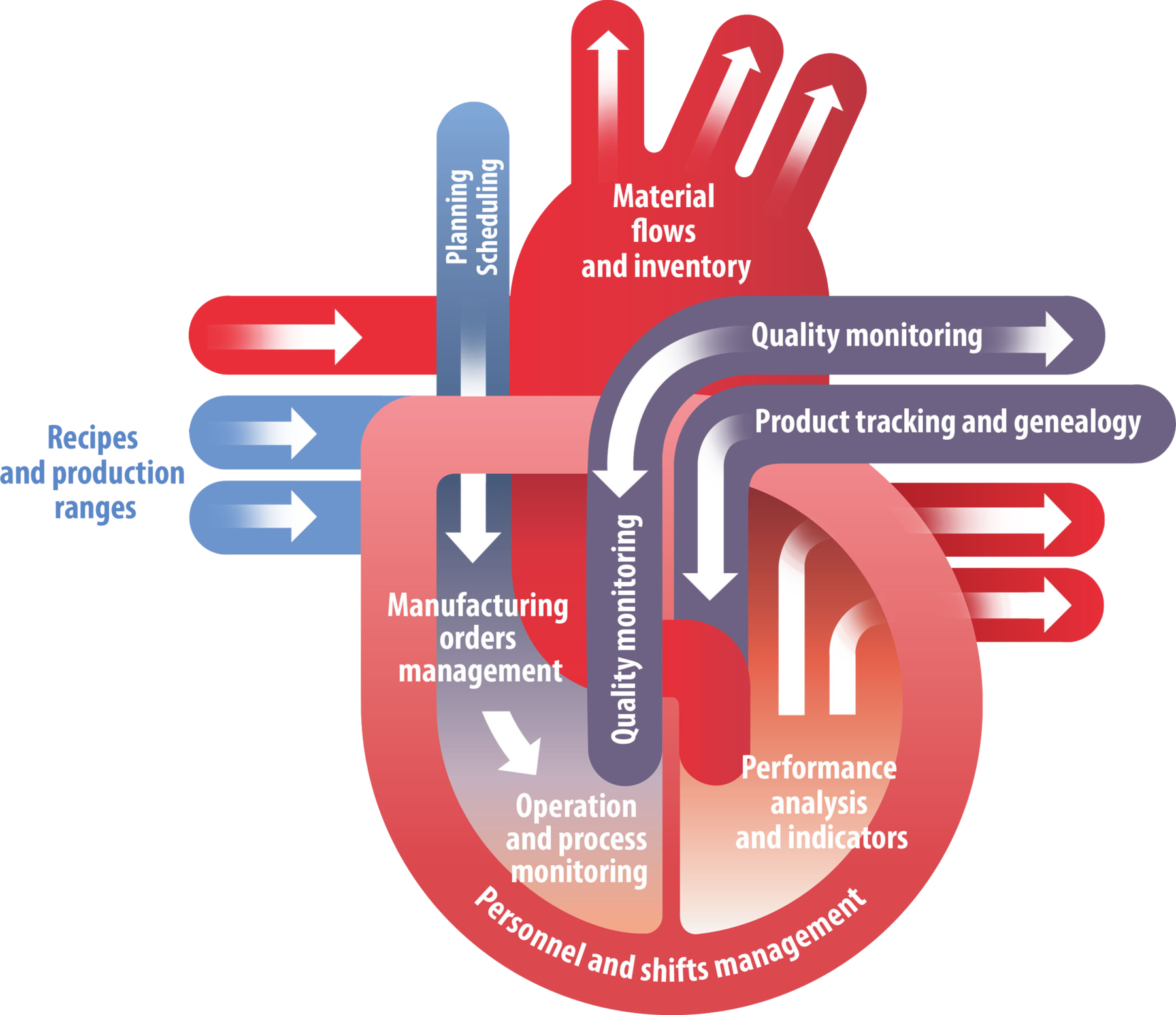
But still, that’s only referring to performance monitoring. The role of an MES is much, much broader than just tracking production: it is more like the conductor, leading all of the different parts in a symphony of production. In the factory of the future, the MES will sequence the manufacturing orders, manage their parallel execution, transmit the manufacturing parameters for each product, no matter how customized, to the machines or the operators, and provide for order traceability. The MES will also detect, in real time, the slightest deviations from the manufacturing parameters or in manufacturing run times, redirecting operations to the most efficient available equipment, as needed. It will also take maintenance needed as a result of a machine problem into account and adjust the production schedule accordingly. To handle this in the factory of the future, it will undoubtedly rely on algorithms from big data and artificial intelligence, although it can already do it using easy-to-implement algorithms.
All of these advances in the factory of the future can be found in the MES concepts developed by MESA in the early 1990s. Released from the challenges of collecting and storing data by new, ultra-high-performance technologies, the MES will deliver on the full potential of its original concept. The technological version of Back to the Future?
Philippe Allot