Définition et calcul du TRS
Le Taux de rendement Synthétique (TRS) est défini par la norme NF E60-182 comme le rapport du temps utile sur le temps requis. Il est destiné à suivre le taux d'utilisation des machines (mesure d'efficacité et du niveau d'utilisation d'un équipement). Le TRS est un indicateur - clé dont le calcul et l'analyse aident à obtenir la performance d'une ou plusieurs lignes de production et les pistes et plans d'action pour l'optimisation. Il intègre l'ensemble des composantes du rendement machine et permet d'avoir une vision synthétique et précise de la performance de production. Il est aujourd'hui l'indicateur le plus suivi dans l'entreprise.

Décomposition du TRS
Autre Calcul du TRS
Il existe une deuxième méthode de calcul qui consiste à multiplier la Disponibilité Opérationnelle (ou Taux de Disponibilité) par le Taux de Performance et le Taux de Qualité :
- Disponibilité Opérationnelle : mesure les pertes de productivité liées aux arrêts non planifiés : pannes, attentes, changement de série...Plus ce taux est important, plus la machine est disponible pour produire.
- Taux de Performance : mesure les écarts de performance dus aux variations de cadence (sous ou sur-vitesse) et aux micro-arrêts. Une machine qui marche au ralenti ou qui cumule des micro-arrêts entraine une baisse de sa performance.
- Taux de Qualité : mesure les pertes de productivité liées à la production de pièces ne répondant pas aux exigences de qualité. Il est donc affecté par le nombre de pièces déclarées non-conformes.
Qu'est-ce que le TRS (Taux de Rendement Synthétique)?
Calcul du TRS
Le Taux de rendement Synthétique (TRS) qui tire son origine du terme anglo-saxon "Overall Equipment Effectiveness" (OEE) revient en fait à diviser le nombre de pièces correctement fabriquées par le nombre de pièces que la machine aurait dû produire dans son temps de production théorique, tout en tenant compte du temps de cycle de chaque pièce. En simplifiant l'opération, il suffit de diviser le temps de production de pièces conformes total par le temps de production théorique total. (soit le Temps Utile / Temps Requis).
Pourquoi chercher à calculer le TRS ?
Le Calcul du TRS est la mesure incontournable pour identifier les pertes, trouver des pistes de progression et augmenter la productivité des équipements de production...pour s'inscrire durablement dans l'amélioration continue.
Il découle de la multiplication des 3 indicateurs cités ci-dessus (Disponibilité Opérationnelle, Taux de Performance, Taux de Qualité), tous compris entre 0 et 100%. Plus le TRS se rapproche de 100%, plus la production est performante. Il s'intéresse en fait à l'identification des pertes responsables de la non-productivité. Celles-ci peuvent être de différentes natures et permettent à l'industriel d'agir en conséquence en :
- Diminuant le temps passé sur une opération
- Diminuant les erreurs des opérateurs
- Diminuant les temps d'arrêt machine
- Améliorant la qualité
- Augmentant la productivité des équipes
- Capitalisez les savoir-faire
- ...
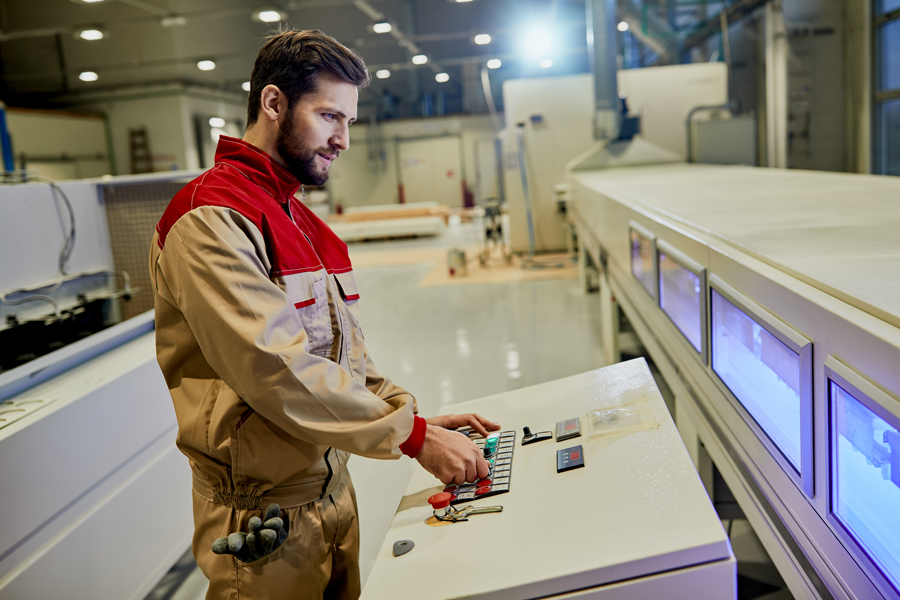
Le TRS : indicateur référence de la TPM (Maintenance Productive Totale)
En identifiant la ressource goulot, c'est à dire la ressource qui est à l'origine du goulet d'étranglement et qui limite ainsi le débit du flux de production, on va pouvoir améliorer le TRS. Ainsi on rapporte le temps utile au temps d'ouverture ou au temps total, on obtient le Taux de Rendement Global (TRG) et le Taux de Rendement Economique (TRE), qui définissent le rendement d'un point de vue plus générique.
La TPM, née officiellement au japon en 1971 est une évolution des méthodes de maintenance qui visent à améliorer le rendement des machines en identifiant en amont les principales causes de défaillance. Une fois détectées, celles-ci sont analysées afin de réduire au maximum les temps d'arrêts non planifiés et improductifs des lignes de production.
Quelques notions sur les temps d'état d'un moyen de production
- Temps total (Tt) : correspond à l'ensemble des états possibles du moyen, temps durant lequel il est théoriquement utilisable (24 heures pour une journée, 68 heures pour une semaine...)
- Temps d'ouverture (To): est égal au temps total auquel on ôte le temps de fermeture de l'atelier. correspond en fait à l'amplitude des horaires de travail, y compris les temps de désengagement comme le nettoyage, les réunions, les pauses, la maintenance préventive...
To = temps total - fermeture de l'atelier - Temps requis (Tr) : période durant laquelle le moyen de production est engagé avec la volonté de produire (y compris temps d'arrêt subis et programmés). Tr = temps d'ouverture - (pauses, réglages, absence de personnel...)
- Temps de fonctionnement (Tf) : temps durant lequel le moyen de production fabrique les pièces (bonnes ou mauvaises). Tf = temps requis - (changements de série, pannes...)
- Temps net (Tn) : temps de fonctionnement durant lequel le moyen de production produit des pièces dans le respect du temps de cycle de référence. Ce temps n'est pas mesurable. Tn = Temps de fonctionnement - écarts de cadence
- Temps utile (Tu) : Temps durant lequelle moyen de production fabrique des pièces de bonne qualité. Tu = temps net - temps passé à faire de la non-qualité
Définition de MES
Un logiciel MES (Manufacturing Execution System) est un système informatique dont l’objectif est avant tout de collecter en temps réel les données de production d'un ilot, d'un atelier, d'une ligne de production... d’une usine, afin d'optimiser le pilotage de la production. Le process est maîtrisé, la qualité et la traçabilité sont irréprochables, la performance industrielle aboutie.
MES et TRS
La plupart des solutions de MES mettent l'accent sur un indicateur très populaire, le TRS (Taux de Rendement Synthétique). Intégrant dans un nombre de 0 à 100 des événements de production aussi divers que les arrêts imprévus, les rejets pour non qualité, les baisses de cadence des machines et leur impact sur la productivité, le TRS (appelé OEE pour Overall Equipment Efficiency par les anglosaxons), apparaît comme l'indicateur de performance universel par excellence, et donc la mesure ultime d'un MES, dont le but est après tout l'augmentation de la performance de production.
En suivant ce raisonnement, le MES se résumerait donc pour l'essentiel au calcul et au suivi du TRS ? Est-ce si simple ?
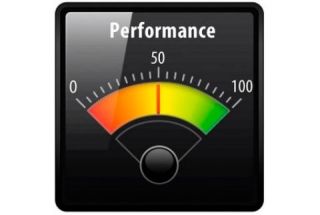
Les clés du succès du TRS
Les clés du succès du TRS tiennent en deux mots : synthèse et comparaison. La plupart des industriels avaient constaté par eux-mêmes que des gisements de productivité étaient présents dans les arrêts des machines pour bourrage, réglages ou autre cause, que les rejets (pièces cassées, produits abîmés ou hors tolérances), obligeaient à des cadences supérieures aux cadences normalement requises pour assurer la production. Mais difficile de mesurer objectivement l'impact d'un arrêt quand il y en a plusieurs dizaines quotidiennement, que certains bloquent totalement la ligne, tandis que d'autres ne durent qu'une minute ou deux. Difficile de quantifier l'importance réelle de quelques centaines de rejets sur une machine qui produit plusieurs milliers d'articles par heure, ou d'une baisse de la cadence durant quelques minutes, à chaque modification des réglages machine...
C'est là que réside l'idée de génie du TRS : ramener toutes les pertes de productivité (arrêts, non-qualités, baisses de cadence) à des temps, y compris pour des paramètres qui n'en sont pas directement au départ (baisse de cadence) ou pas du tout (rejets pour non qualité) !
De cette manière, on peut comparer le "temps utile" (temps réellement passé à produire des produits bons) au temps idéal pendant lequel on aurait pu théoriquement en produire si aucune de ces pertes de productivité n'était survenue.
Par définition, le rapport entre ces deux temps est un nombre entre 0 et 1, qui peut s'exprimer en pourcentage : c'est le TRS. Et le miracle est que ce taux synthétique va permettre une comparaison entre deux lignes qui n'utilisent pas les mêmes machines et le même personnel, qui n'ont pas les mêmes durées d'utilisation, qui ne se trouvent même peut-être pas dans le même pays.
Le rêve du responsable de site qui veut montrer que son usine est la plus performante, mais aussi celui du contrôleur de gestion ! Pour autant, faut-il voir dans le TRS la quintessence du MES, ce qui laisserait penser, entres autres, que les autres fonctions du MES sont beaucoup plus accessoires ? Certainement pas !
Simplicité de mise en oeuvre du TRS
L'un des principaux arguments en faveur de la mise en place d'un TRS est sa simplicité de mise en oeuvre. Cet argument est légitime, pour autant qu'on utilise un logiciel adapté. Dans le même temps, on peut se demander si un logiciel est nécessaire : le calcul du TRS semble si simple que sa mise en place à l'aide d'un outil comme Excel paraît suffire...
L'utilisation d'un logiciel adapté s'impose pour deux raisons:
La première est que la simplicité du calcul du TRS n'est qu'apparente. Les formules de calcul du TRS et de sa décomposition (Taux de disponibilité, Taux de performance, Taux de Qualité) ne sont pas très complexes, mais reposent sur des temps. Pour que ceux-ci soient exacts, un système temps réel, et non une saisie a postériori, est la seule solution réellement fiable. De plus, si le calcul du TRS d'une machine isolée est simple, le calcul pour une ligne de production où les machines dépendent les unes des autres est plus délicat. Il fait intervenir les notions d'arrêts propres (dus à la machine elle-même) et d'arrêts induits (manque matière dû à l'arrêt ou à la sous-cadence d'une machine en amont). Dans ce cas, les risques d'interprétation erronées d'un calcul simpliste sont importants.
La seconde est que l'objectif est le gain de productivité, et non l'inverse ! En plus d'être sources d'erreur, les saisies d'informations pour le calcul du TRS sans l'appui d'un logiciel dédié sont très chronophages, et distraient les opérateurs de leur objectif premier de production. Un logiciel dédié limite au maximum ces saisies et les facilite lorsqu'elles sont indispensables (appui d'un simple bouton, par exemple, pour identifier une cause d'arrêt).
Aussi est-il essentiel que les industriels mettent en oeuvre un outil de mesure et de suivi du TRS pour améliorer leur productivité. Mais doivent-ils pour autant s'arrêter là ?
Etre conscient des limites du TRS
Pour essentiel, voire indispensable qu'il soit, l'indicateur TRS n'est pas sans défaut, et il faut être conscient de ses limitations.
Tout d'abord, même s'il intègre de nombreux paramètres des événements de production, il ne les intègre pas tous. Par exemple, dans la prise en compte des non-qualités, seul le temps perdu à produire des articles mauvais est intégré dans l'indicateur, mais la perte de matière correspondante (si elle n'est pas recyclée) et sa valorisation ne sont pas intégrées.
Aussi, de nombreux industriels entretiennent aux côtés du TRS d'autres indicateurs (souvent appelés KPI pour Key Performance Indicators), permettant de suivre les pertes matières, les consommations d'énergie, etc. Il est donc important que le logiciel de MES ne se borne pas au calcul du TRS et des indicateurs qui en dérivent directement, mais soit aussi capable de délivrer d'autres indicateurs de performance, ou permette de les construire aisément.
Le MES : le TRS et bien plus encore
Système, le mot est donné, car dans la multiplicité des données collectées sur une installation de production, seul un système structuré - le standard ISA-95 aide grandement à cette structuration - permettra de les utiliser efficacement pour déterminer les voies d'optimisation les plus prometteuses. La capacité du logiciel MES à traiter, dès sa mise en oeuvre ou progressivement ces différentes voies d'optimisation est essentielle.
L'indicateur TRS est une mise en application de la méthode DMAIC (Define, Measure, Analyze, Improve, Control) que l'on gagne à étendre à tous les axes de la production qui peuvent être pris en compte par un véritable système MES. A cet égard, le TRS est un indicateur emblématique de la démarche générale d'amélioration continue qui est la clé non seulement de la productivité, mais de manière plus générale de la compétitivité des industriels, laquelle englobe en particulier l'innovation.
On touche d'ailleurs là une limitation de fond, qui tient à la définition même du TRS, que l'on comprend mieux avec la dénomination anglo-saxonne OEE Overall Equipment Efficiency (littéralement efficience globale des équipements). Le TRS mesure la productivité des équipements, une mesure nécessaire, mais rarement sufffisante. L'efficacité globale d'une usine ou d'une unité de production va aussi dépendre du personnel (temps d'exécution des opérations manuelles ou semi-automatisées) et de l'efficacité du process dans son ensemble. Si ce process n'est pas linéaire (cas des process semi-continus ou batch), ou si de multiples chemins sont aménagés pour l'exécution d'opérations en parallèle, l'applicabilité de ce type d'indicateur est délicate, voire impossible. L'optimisation de l'exécution par un ordonnancement ou une allocation dynamique des ressources, une maîtrise des recettes et du procédé, fournira une voie plus puissante d'amélioration de la performance, dont le système MES devra également disposer.

La Solution MES COOX d'ORDINAL Software vous permet de mettre en oeuvre de façon intégrée et modulaire toutes les voies d'optimisation de la production, quelles que soient celles que vous choisissez de privilégier.
Améliorez son Taux de rendement Synthétique grâce au MES
Optimiser le temps passé sur une machine
Les temps d'arrêt planifiés ou non planifiés pénalisent la productivité. Il est donc important de les comptabiliser et de les analyser car ils ont un impact non négligeable sur le Taux de Rendement Synthétique (TRS).
Les arrêts induits correspondent à un non-fonctionnement de la machine (manque de personnel, saturation de pièces, défaut d'énergie, défaut d'approvisionnement...).
Les temps d'arrêt propres quant à eux regroupent les temps de panne, les temps d'arrêt d'exploitation et les temps d'arrêt fonctionnels (arrêts planifiés).
Digitalisation des opérations
En digitalisant les causes d'arrêts plutôt que de les saisir sur papier et en transmettant ces informations en temps réel depuis sa machine, l'opérateur gagne du temps et participe à l'optimisation des délais d'intervention. Résultat, l' industriel accroît sa productivité.
L'aide aux opérateurs
Afin de réduire les temps d'arrêt , il est tout aussi important de guider l'opérateur dans l'exécution de ses tâches, en affichant par exemple les différentes étapes des opérations à effectuer, avec un état progressif de leur réalisation, avec l' intégration des instructions, des plans, des vidéos, des photos...
Cela permet d'éviter l'interprétation et de limiter au maximum l'erreur humaine.
Maintenance préventive
La maintenance préventive est aussi un élément majeur qui a une incidence sur la productivité. En anticipant les pannes potentielles et en garantissant le bon fonctionnement des machines, celle-ci permet de réduire les pannes, d'assurer la sécurité, de réduire les temps d'arrêt et donc d'améliorer la production.