With the avalanche of technologies that is now invading the industry in what is commonly called the Factory of the Future - 3D Printing, Cloud, Big data, AI, IoT, Virtual Reality, Digital Twin, etc. - there is no doubt that the industry is expected to experience many changes in the years to come.
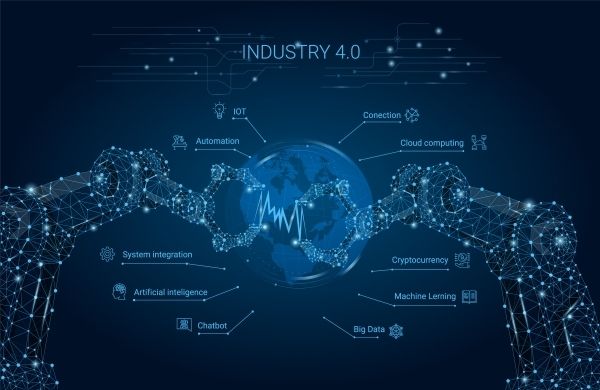
Changes with different impacts
But all these changes are not similar. Some may be simple in principle, such as changing a type of machine, or a communication technology with a faster technology, and yet entail very high costs, because all the equipment (machines, connections, routers, servers, ...) must be modified.
On the other hand, these changes often require adequate preparation and support.
MES, driving the digital transformation
The set up of an MES solution belongs to this second category. Even if we can start with a simple step, like setting up a measure of OEE indicators, the MES can go much further and fully support the digital transformation of the factory towards digital continuity. Such a project is therefore not limited to providing managers with a real-time state of production and its level of efficiency: it transforms the daily life of all production stakeholders, in particular operators.
The potential gains associated with digital continuity and the workshop agility are these: limitation of errors, reduction of range change times, anticipation of critical situations, predictability of production, etc. They are immense and very much superior to those brought by the "accounting" measure of productivity. It is still necessary to move in the mind of all the actors of the production the MES system from the box "additional tasks" to the box "real production aid" then to the box « how have we been able to do without until now? »