Les avis sont très partagés lorsqu'on essaie de distinguer clairement MES et MOM. Certains pensent que le MES est un sous-ensemble du MOM, d'autres pensent qu'ils définissent un espace fonctionnel différent, d'autres enfin qu'ils décrivent exactement la même chose...
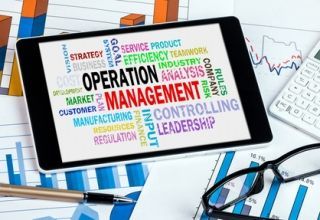
Origine
L'acronyme MES a été inventé au milieu des années 1980, le MOM est arrivé un peu plus tard et semble non seulement décrire un espace un peu plus large mais surtout un ensemble d'opérations que l'on retrouve dans l'ISA95 en termes d'architecture et de fonctionnalités.
Grossièrement, même si ces domaines étaient présents dans les fonctions MES originales, le MOM a mis l'accent, au-delà du domaine de la production, sur ceux de la qualité, de la maintenance, et des stocks d'atelier.
Evolution
Le MES qui couvre tout autant la norme ISA-95 peut aussi être appréhendé différemment dans la mesure où il désigne avant tout, comme son nom l'indique, un "système", c'est à dire un outil, un logiciel qui permet en fait d'exécuter les opérations du domaine du MOM.
Les premiers systèmes MES offraient peu de flexibilité et avaient parfois du mal à s'adapter à l'évolution des besoins des entreprises.
En réponse à ces besoins croissants, au niveau de l'atelier de production, mais aussi au niveau de la qualité, de la gestion des stocks, de la maintenance..., le terme MOM est apparu comme une évidence pour désigner cet élargissement de fonctionnalités attendues.
Le terme de Gestion des Opérations de Fabrication a ainsi été aménagé, les différentes activités ont été détaillées ainsi que les processus opérationnels.
Domaine commun
Mais finalement, MES et MOM se référent bien tous les deux au même domaine : la gestion et le pilotage des opérations de fabrication, dans le respect des normes de modélisation et d'intégration (ISA95 et ISA88).
Un système MES va donc par définition, exécuter en temps réel les opérations de fabrication (MOM) et permettre à l'industriel de s'inscrire dans une démarche d'amélioration continue grâce par exemple à :
- une meilleure diffusion des informations (synchronisation, coordination et centralisation des flux)
- une simplification des processus de fabrication
- un respect des conformités réglementaires
- une gestion des stocks maîtrisée
- un suivi qualité optimisé
- une traçabilité du procédé et des produits systématique
- l'analyse et l'amélioration régulière des performances