Lancés dans les années 90, les systèmes MES se sont donnés dès l’origine des ambitions importantes dans l’optimisation en temps réel de la production. Dans l’esprit de ses promoteurs, le MES serait rapidement à même non seulement de prendre en charge l’ensemble des procédures d’exécution des opérations et de les tracer, mais aussi de les optimiser de manière quasiment transparente pour les opérateurs et les exploitants.
L’augmentation des performances et l’accessibilité accrue des technologies d’Intelligence Artificielle rendent plus que jamais actuelles les ambitions initiales de ces solutions. Ce thème a été développé par Philippe Allot lors d'une conférence organisée par l'ISA95 sur le thème de l'Intelligence Artificielle et de l'Industrie du Futur. Au travers de quelques exemples, nous allons essayer de mesurer l’apport décisionnel en temps réel susceptible d’être engendré par l’IA dans le domaine de l’anticipation des dérives d’un procédé, le contrôle de la qualité ou la maîtrise des paramètres garantissant l’optimisation globale de l’exécution d’un procédé.
Dans la pratique, la planification détaillée des fabrications, les problématiques d’acquisition des informations tant au travers des automatismes que par saisie, l’orchestration des opérations tant automatiques que manuelles, le suivi des contrôles de qualité et de conformité et la mesure de la performance par des indicateurs adaptés, ont nécessité des efforts importants et leur prise en charge de manière dématérialisée est aujourd’hui le principal apport des solutions MES. L’optimisation, quant à elle, repose pour l’essentiel sur l’analyse humaine de l’ensemble des indicateurs élaborés par les solutions MES/MOM.
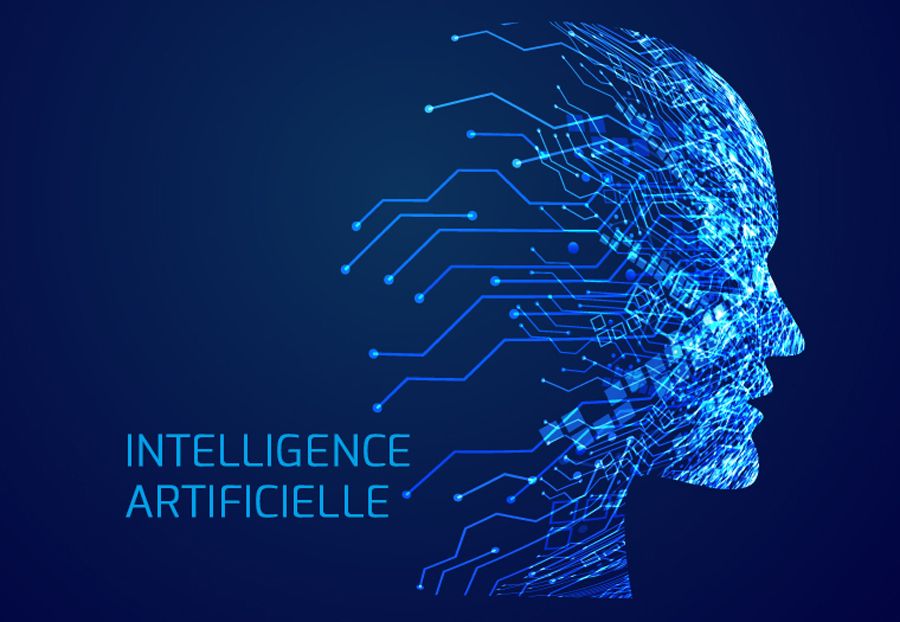
IA et MES : objectifs atteints et objectifs à atteindre
Pourquoi cela a-t-il un sens d’appliquer les technologies d’IA au MES et comment cela peut-il se faire ?
Il y a encore peu de temps, nous avions affaire à deux mondes qui s’ignoraient totalement et ce pour plusieurs raisons:
- Avant la déferlante de l’industrie 4.0 et de l’Industrie du futur, l’industrie avait plutôt une attitude « mainstream », très conservatrice en matière d’IT. L’intégration de technologies nouvelles a eu tendance à se faire uniquement lors de la construction de nouvelles usines ou lors de revamping significatifs.
- Une seconde raison tient au fait que l’on a beaucoup insisté sur l’apport de l’IA pour traiter des données massives non structurées, comme des images, des messages textuels ou vocaux. Le MES peut aussi traiter des volumes de données importants, mais elles sont fortement structurées. Pourquoi dès lors employer de l’IA ? Sans oublier que le Big Data et le cloud posent aussi le problème de la confidentialité des données.
- Sur le plan pratique, l’IA dans l’industrie s’est plutôt focalisée sur des problèmes très spécifiques, sans solution classique et à fort potentiel de gain : par exemple, notre partenaire en IA ProBayes s’est attaqué au problème du développement de champignons sur les anodes sur un procédé électrolytique.
- Enfin l’IA comme beaucoup de technologies actuellement sous les projecteurs, met surtout l’accent sur les données. « Vu d’avion », le MES peut apparaître comme un simple collecteur de données, au même titre que l’IOT par exemple, en faisant abstraction, entre autres, de tout l’aspect fiabilisation et contextualisation des données.
Les obstacles à surmonter
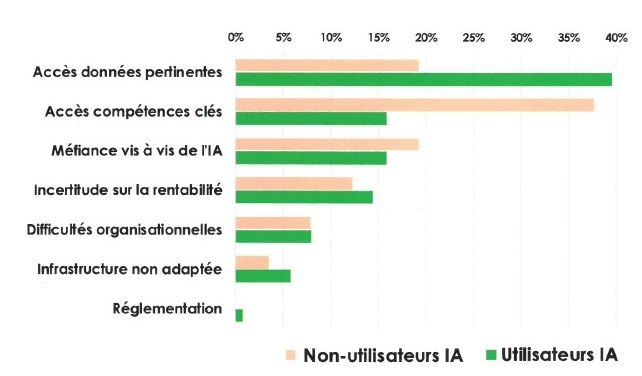
Une enquête a été réalisée par l’Association des Centraliens et le MEDEF. Pour l’industrie, elle montre que le principal obstacle (40%) pour l’IA est l’accès à des données pertinentes. Cet obstacle est sous-estimé (20%) par les industriels qui n’ont pas mis en œuvre d’IA, lesquels ont tendance à surestimer le problème des compétences clés.
Pourtant, il y a de bonnes, et même de très bonnes raisons d’allier au MES les capacités de l’IA. En effet, les solutions MES ont parfaitement atteint un certain nombre d’objectifs :
- Planification détaillée des ordres de fabrication en fonction des contraintes
- Gestion et assignation des ressources en fonction des contraintes
- Exécution et suivi des opérations
- Traçabilité procédé et produit
- Indicateurs temps réel de performance (KPI)
- Gestion des flux logistiques
- Aide aux opérateurs
- Aide à la maintenance
Mais à côté de cela, un certain nombre d'autres objectifs restent à atteindre comme par exemple ceux de :
- Modifier la planification pour compenser les interruptions de production
- Exécuter des simulations hypothétiques pour déterminer les goulots d'étranglement et/ou la capacité d’exécution d’une production future
- Déterminer pourquoi les « golden run » sont obtenus
- Prédire des situations d’urgence
- Optimiser de façon automatique le procédé et les procédures en fonction des résultats d’analyse
- Prédire les résultats d’une production en fonction de son état actuel et des exécutions passées
- Optimiser automatiquement la qualité
- Optimiser automatiquement les flux
La plupart de ces objectifs figurent depuis 2005 (et probablement avant) comme fonctions MES dans les travaux de l’ISA-95. Leur définition même (analyse, prédiction, optimisation) les place dans le champ d’application de l’IA ! Les ambitions initiales du MES ne sont donc pas si éloignées de l'IA !
Apports possibles de l'IA pour le MES/MOM
Parmi les contributions que peut apporter l'IA au MES, on peut ici en citer au moins 3, à titre d'exemples.
Maintenance prédictive
Le domaine du MES où l’apport de l’IA a été le mieux exploré jusqu’ici est sans doute le domaine de la maintenance prédictive.
Un petit rappel : la maintenance d’un équipement consiste à maintenir son bon état de fonctionnement. Traditionnellement, deux types de maintenance sont mises en œuvre :
- La maintenance corrective : on répare ou on change l’équipement quand il tombe en panne. C’est admissible si le temps de réparation est court et les conséquences de la panne faible (si l’avion tombe ou que son train d’atterrissage se casse c’est plus embêtant)
- La maintenance préventive systématique : on contrôle ou on change l’équipement de manière systématique, au bout de tant d’heures d’utilisation par exemple, avec peut-être un guide statistique comme le MTBF.
La maintenance préventive systématique a bien sûr un coût, et n’est pas nécessairement optimale. On peut passer du temps à changer préventivement un équipement qui aurait pu continuer à fonctionner le double du temps. A l’inverse, un équipement présentant des défauts de fabrication peut tomber en panne bien avant le cycle de remplacement.
La maintenance prédictive fait l’objet d’une norme qui détermine que la maintenance conditionnelle doit être exécutée en suivant les prévisions extrapolées de l’analyse et de l’évaluation de paramètres significatifs de la dégradation de l’équipement. Ses objectifs : optimisation de la maintenance préventive mais aussi réduction des facteurs de défaillance.
Si les paramètres sont nombreux, l’IA (apprentissage, corrélations, modélisation) va permettre d’identifier les signaux (forts ou faibles) annonciateurs de défaillance et les prédire. Ces problématiques sont très générales et des grands constructeurs comme Siemens (MindSphere) envisagent de les mettre à disposition en plateforme.
Prévention des dérives du procédé et de la qualité
Par ailleurs, pour mieux maîtriser leur procédé et la qualité des produits de façon plus efficace que par un simple contrôle des tolérances admissibles, les industriels ont cherché à développer des méthodes destinées à prévenir les dérives, et par là à anticiper voire éviter les dysfonctionnements des équipements ou les non-qualité. Jusqu’ici, ces méthodes se sont essentiellement appuyées sur des approches statistiques (Statistic Process Control, Statistic Quality Control) ne prenant en compte que le paramètre à surveiller.
Les différentes méthodes et règles appliquées (échantillonnage, cartes de contrôle X barre, règle des 7 points consécutifs croissants, etc.) supposent, explicitement ou implicitement, des propriétés particulières des procédés qui ne sont réellement vérifiées que pour quelques types d’évolutions (usure mécanique, décalage des réglages par vibration, etc.). Ces méthodes perdent une grande partie de leur pertinence si le résultat mesuré dépend de plusieurs paramètres, et pour les procédés dont les lois ne sont pas linéaires.
Or c’est le cas dans de très nombreuses industries, comme les industries agroalimentaires de transformation, la chimie et les cosmétiques, la pharmacie, les bio-industries, les industries de procédés complexes, etc...Une fonction d’IA apte à prendre en compte les paramètres pertinents influant sur le procédé et/ou la qualité des produits sera d’un apport considérable pour ces industries. Elle permettra à la fois d’identifier des paramètres (ou combinaisons de paramètres) influents jusqu’alors inconnus ou négligés, et permettra d’orienter au mieux les travaux d’amélioration de procédés.
Certaines productions ne sont pas poursuivies en deçà d’un certain rendement (exemple textile). Prédire le rendement permet d’interrompre au plus tôt la production afin de limiter le gaspillage ou, si les procédés de fabrication le permettent, d’opérer des reprises et autres corrections sur les produits avant qu’il ne soit trop tard. Le modèle de l’IA pourra aussi évoluer en cas d’évolution du procédé.
Indicateurs de performance de nouvelle génération
Enfin, de nombreux outils d’analyse de la performance ont été mis en place dans les dernières décennies, tels que le TRS. Ils ont permis le plus souvent la mesure des pertes de productivité et la classification des causes d’arrêts de production en fréquence ou en durée (diagrammes de Pareto).
Sur la base de ces résultats, les industriels ont cherché à réduire les causes d’arrêts les plus fréquentes ou les plus pénalisantes. Si la réduction de certaines causes d’arrêts s’est révélée aisée, certaines se sont révélées plus réfractaires. On retrouve cette difficulté dans les expressions employées par les opérateurs de production chevronnés « Le produit A passe toujours mal sur cette machine ! ». Certes il y a fréquemment des bourrages, mais à quoi les attribuer ?. L’opérateur chevronné a fait une première analyse intuitive, en corrélant ces difficultés au produit fabriqué. Mais l’IA permettra certainement d’aller plus loin, en identifiant la ou les caractéristiques du produit A liés à ces problèmes. La démarche est donc l’extension des principes de maintenance prédictive à l’ensemble des arrêts de production (défaillance d’équipement ou autre) et la mise en évidence des causes profondes par une analyse multidimensionnelle.
A terme, on peut penser que de nouveaux indicateurs « prédictifs » viendront remplacer les indicateurs classiques de type TRS.
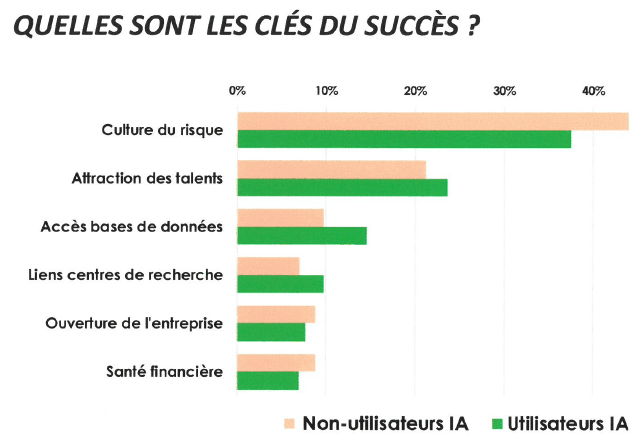
Ainsi donc, nous avons vu que jusqu’ici, IA et MES avaient plutôt suivi des chemins différents.
Pourtant, en reprenant quelques objectifs donnés dès le départ au MES, mais non encore atteints, nous avons vu que l’IA faisait presque partie de l’ADN du MES. Aujourd’hui, il y a matière à être plus concret, comme nous en avons vu quelques exemples.
Un autre point que mettent en évidence les experts de de l’IA est l’importance d’une boucle d’usage des données. On dit parfois que l’on est « assis sur un tas d’or » parce que l’on a beaucoup de données. C’est faux, c’est l’usage des données qui va en montrer la pertinence et va permettre d’en collecter d’autres, plus utiles pour l’analyse de l’IA, et cette boucle d’usage, c’est précisément le MES qui la fournit.
L’IA va certainement permettre de donner un élan supplémentaire au MES/MOM, qui au fond était là dès le départ. Cela ressemble à un « retour vers le futur » du MES.